VACUUM DIE CASTING
> VACUUM DIE CASTING > Introduction to vacuum die casting
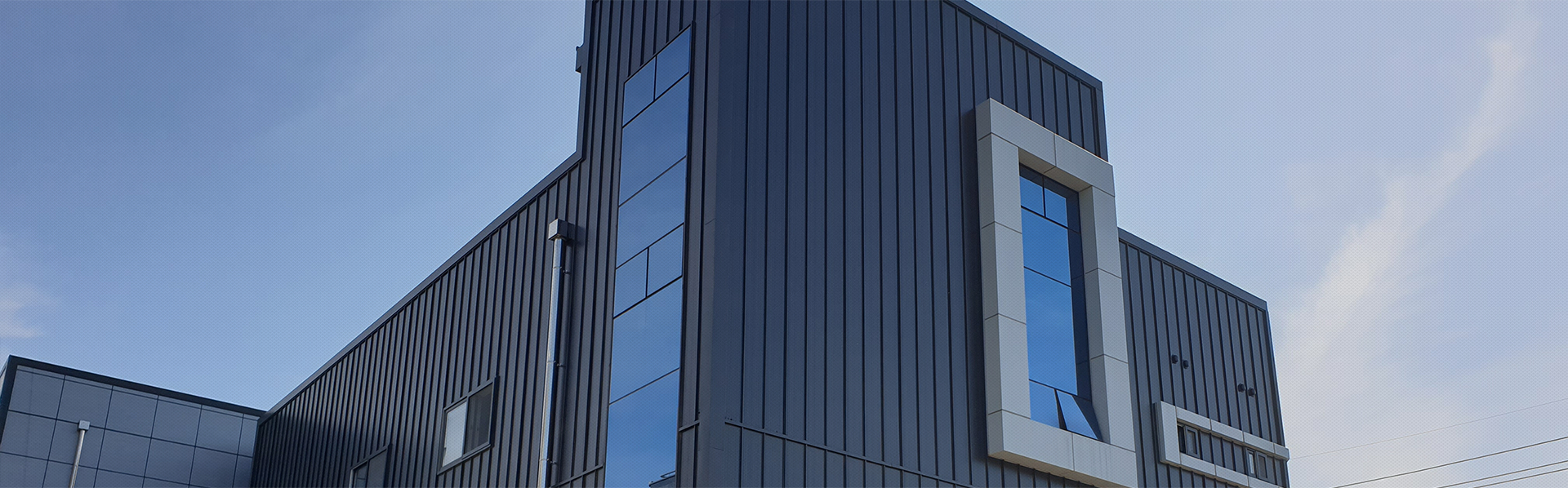
> VACUUM DIE CASTING > Introduction to vacuum die casting
Vacuum die casting method and overview
What is vacuum?
Vacuum refers to a state in which the gas pressure of a space is lower than atmospheric pressure, and the standard atmospheric pressure based on sea level is 1 atmosphere pressure, and the sea end unit is as follows.
1atm (1 atmosphere) = 1.0332 kg/㎠ = 1013 mbar = 760 mmHg = 101.325 KPa
Overview
The charging time of the die cast is very short compared to that of general casting. In addition, there is not enough time to exhaust gas from existing air vents to improve quality and reduce defect rates as the shape of the product becomes increasingly complex. Due to the injection effect of the gate during high-speed casting, a large part of the molten metal comes into contact with the internal air and gas of the cavity, which affects the residual gas in the sleeve and affects the quality of the product. Accordingly, the purpose is to improve the quality of the product and solve problems such as existing bubbles, unformedness, and contraction by more actively exhausting air and gas inside the cavity using a vacuum device.
Vacuum die casting method
In the existing die casting method, internal quality defects due to fast charging have long been a concern. This device is a device that forcibly exhausts gas generated during air and hot water by suctioning the cavity inside the mold through vacuum. As a result, problems such as a decrease in the quantity, size, and unformed internal bubbles have been solved and are used in many areas such as automobile parts, oil pumps, water pumps, head drums, case covers for devices, and thin products.
In general, vacuum valve blocks show better vacuum than Chilvent blocks at the same suction volume, but higher vacuum does not mean that a product comes out better, and some molds do not change product quality even when actual vacuum blocks and Chilvent blocks are used alternately. Chilvent molds should remove oil stains, foreign substances, burrs, etc. at least once a day on Chilvent stairs, and vacuum valve blocks should also be disassembled at least once a day to clean, check for scratches on vent pins, operating pins, etc. In some cases, LOT defects occur by working with the lacquer vent covered with dirt (reducing vacuum effect), and in some cases, vent pins or operating pins of the vacuum valve are worn out to the vacuum valve block, so the entire block needs to be replaced.
Currently, Diecast does not use only one casting method, but also vacuum casting and squeeze as needed, and other hot water management, warm-aircraft use, jet cooler, release agent selection, and casting condition management are all items that users should consider for the best quality.
Vacuum work order
A schematic diagram
Work flow
01
Formation
closure
02
Melting
water
charging
03
Emission
04
Chill
05
Formation
open
06
Product
pick-up
07
Spray
Vacuum signal setting
※ Vacuum start time is different for molds and products, but in small sizes under 350 tons, the plunger usually starts blocking the molten inlet and gives -30-300mm in the high-speed section as it goes larger, and the melt filling rate inside the cavity is 10~30%, calculating the sleeve diameter and molten amount to specify the plunger stroke position.
Considerations for Vacuum Die Casting Operations
Multi-stage vacuum die-casting method
It is applied to reduce the phenomenon of hot water wrinkles, surface defects, and molten metal flow changes that occur when suctioning with high vacuum pressure from the start of vacuum.
Since the plunger stroke is less than 500mm below 500 tons, the time to see the effect is very short. -The injection time is around 1.0 sec including relatively low speed and high speed - it is recommended to use it from 1250 tons or more to large size. If the low speed is slow, such as 0.1 m/sec, it can also be applied to molds of 500 tons or less. The purpose of using multi-stage vacuum is to reduce the change in molten flow inside the cavity by smoothly passing from low pressure to high vacuum without rapidly changing the vacuum pressure inside the cavity. The suction time and vacuum pressure of the low vacuum section may be freely set, respectively.
* Multi-stage vacuum is a unique technology in the DAEKI INDUSTRY.